- The edge is placed flat against the grinding wheel surface
This is the first step in the bit’s position relative to the grinding wheel. Some inexperienced operators lean on the grinding wheel and start sharpening the edge before they even straighten it out. This must not wear well. The “edge” here is the main cutting edge. “Leveling” means that the main cutting edge of the sharpened part is in a horizontal position. “Wheel surface” refers to the surface of the grinding wheel, “against” is slowly close to the meaning. At this point, the drill bit cannot touch the grinding wheel;
- Oblique drill shaft repair sharp Angle
Here refers to the axis of the bit line and the location of the relationship between grinding wheel surface, “Sharp Angle” is the half of the point Angle 118 ° ± 2 ° , it’s about 60 °. This position is very important, which directly affects the size of the point Angle of the drill bit, the shape of the major cutting lip and the chisel edge Angle. Do not neglect to lay down the bevel Angle in order to lay down the cutting edge, or to lay down the axis in order to lay down the cutting lip. These errors are common in practice. At this point, the drill bit is ready to contact the grinding wheel in the correct position;
- From the edge to the back of the grinding
This refers to the grinding of the bit’s edge slowly along the entire back surface, starting from the edge of the bit. This facilitates heat dissipation and sharpening. At this point, the bit can gently contact the grinding wheel for a small amount of edge grinding. When grinding the edge, observe the uniformity of spark, adjust the hand pressure in time, and pay attention to the cooling of the drill bit. When the edge grinding starts again after cooling, continue to set the position.
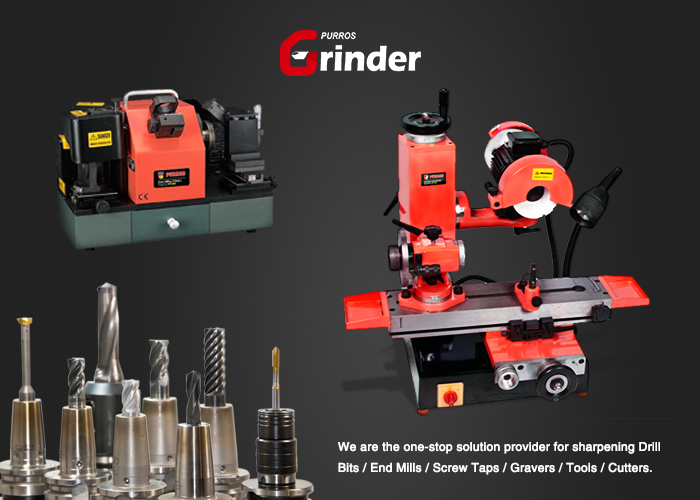
The Universal Tool Grinder is offered by Purros Machinery Co., Ltd., a professional OEM/ODM tool grinder manufacturer and supplier, End Mill Grinder, Twist Drill Grinder, Lathe Cutter Grinder, Carving Tool Grinder, Drill Sharpener, Universal Grinder, etc.
Manual grinding of high speed steel bit is subject to human factors. Manual grinding will result in a large error of the drill bit due to the difference between human experience and personal intuition. But machine repair and grinding completely avoid this problem. Drill bit grinding machine is more accurate, and the error is small, the human factors are relatively small. Operators do not need to go through professional drill grinding training can be on duty. The operation of the drill bit grinding machine is very simple and the efficiency of the drill bit grinder is very high. Therefore, now many companies that use drill bits choose to buy a drill bit grinding machine to repair the damaged drill bits, which saves a lot of cost. Our tool grinding machines are of very good quality and have been well received by our customers in the market. Welcome to inquire purchase.