Here’s some quick sharpening tips.
Keep the glasses on use the guard practice with your crappiest tools first. So when you get the hang of this when you nicer your better drill bits you got some skills. We’ll make this better as far as we can.
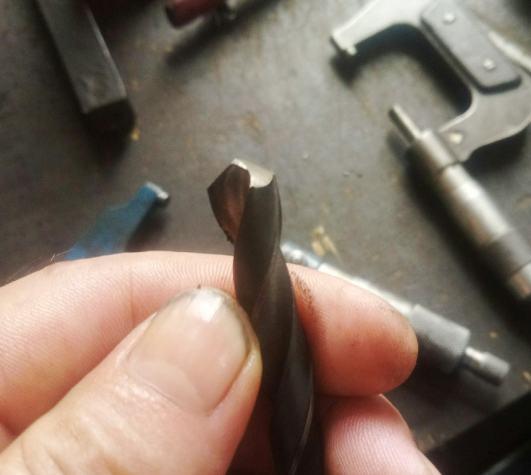
Sharpen the skills of the drill bit, how to repair and grind the drill bit, how to repair and grind the drill bit, how to repair and grind the top Angle of the drill bit, how to repair and grind the Leading Edge of the drill bit
Here we are at bench grinder. What we’re going to do? We’ve got a bad drill bit and you’ll notice the leading edge the top. Leading edge is what does all the work of a drill bit. When we hit bad material, it doesn’t remove material anymore. Eventually it’ll blew and ruin the drill bit if we want to take off some of the material on the back side.
Next we will going to show that I do to polish the front.
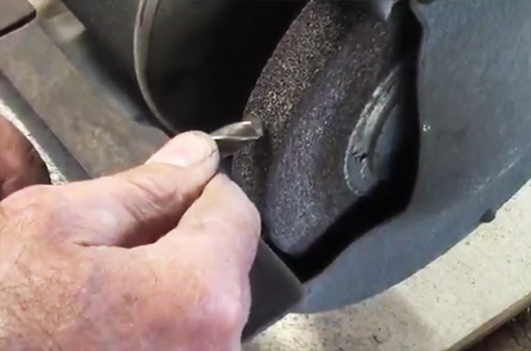
Sharpen the skills of the drill bit, how to repair and grind the drill bit, how to repair and grind the drill bit, how to repair and grind the top Angle of the drill bit, how to grind front of the drill bit, how to repair and grind the Leading Edge of the drill bit
We’re gonna hold it just for a second or two like that in the Leading Edge. To clean this leading edge up the face and then we’re gonna grind on the backside of the bit slowly. Bringing the bit down until we see sparks hit the front. We’re gonna use all the side of the wheel.
When you’re doing this you look down and see where the center is and when you do one side. And you got your hands in position. You don’t look at it.
Then go back down and do it again. What happens as you lose your hand positioning so to do you look down this leading edge. And you watch the sparks. And you just touch it and you flip it over you don’t move your hands. See what that did is it gave me a clean Edge we can see my surface.
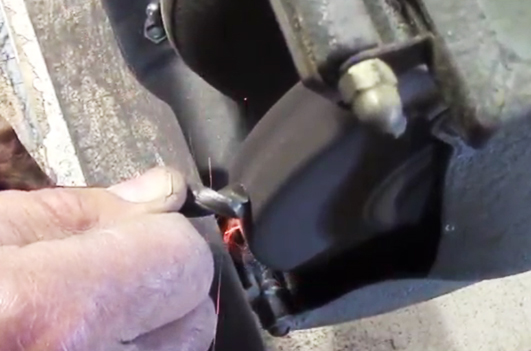
Sharpen the skills of the drill bit, how to repair and grind the drill bit, how to repair and grind the drill bit, how to repair and grind the top Angle of the drill bit, how to grind front of the drill bit, how to repair and grind the Leading Edge of the drill bit
When we are going to sharpen now. We can see how grounded. We swallow they bring it down until we see some sparks coming off the front. The material going down now we don’t get to look at it. We go back off the back. We rotate it to do the other half. Then we start at the back. We go down they see well when we get near the tip. We push less and less hard. So there is their cut. It’s going downhill. So the leading edge is the highest point.
It’s sharp as a razor right now. And both side look about the same decides. A little worse than the other. And we checked for center the other trick with. When we do the face of the grinding so wide. This is here we’re going to narrow that up a little bit. So when this goes on a piece of metal and it’s spinning. It’s not wandering all over the narrower that is better it stays on your mark. It doesn’t wonder as you’re trying to drill. So that just got narrower if you know what we are looking at you see. Its narrower now in the center as we get sharper. We’ve pushed less higher. So we actually have little too steep of a relief angle on this side.
These are some tips of quick sharpening drill bit. This method of grinding drill bits depends entirely on experience and feeling. We recommend our drill bit grinder products to you. It can finish drill grinding easily and correctly. Welcome to consult our products.